How is laminated glass made?
Share this blog:
Laminated glass is used wherever extra safety is required. But how is it made? Find out in our guide.
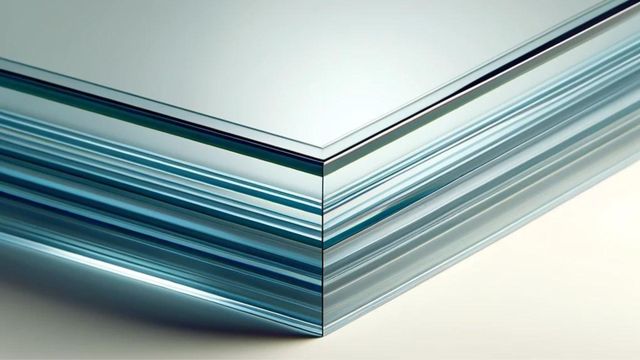
عالمٌ بلا زجاجٍ مُصفح سيكون أكثر خطورة. لماذا؟ لأن هذه المادة الأساسية مُصنّعة بطريقةٍ تمنعها من التفتت، بل تحافظ على ثباتها الهيكلي.
تخيل فيلم أكشن. تنفجر الإطارات، وتشتعل السيارات، لكن الزجاج الأمامي يبقى سليمًا مهما تشقق. كل هذا بفضل الزجاج الرقائقي.
ولا يقتصر استخدامه على زجاج السيارات الأمامي، بل يُعدّ الزجاج الرقائقي أيضًا مادة أساسية في واجهات المتاجر والأبواب والزجاج الهيكلي، وفي أي مكان يُنصح فيه باستخدام زجاج الأمان أو يُشترط استخدامه.
لكن لماذا ينكسر هكذا؟ الأمر كله يتعلق بعملية التصنيع.
أساسيات الزجاج الرقائقي
الزجاج المصفح هو نوع من الزجاج المشطوف. تُؤخذ لوحان من الزجاج - غالبًا ما يكونان مقوّيين - وتُوضع بينهما طبقة من الفينيل.
هذه الطبقة من الفينيل تُشبه الزبدة في صنع ألواح الزجاج. إنها زبدة قوية ولزجة تُثبت الأسطح معًا وتمنعها من التكسر إلى قطع كبيرة.
ما هي العملية؟
تختلف العملية الدقيقة من مكان لآخر. ولكن عادةً ما تبدو عملية تصنيع الزجاج الرقائقي على النحو التالي.
أولاً، تُقطّع ألواح الزجاج حسب الحجم المطلوب باستخدام آلة CNC. هذه آلة تُدار بواسطة الكمبيوتر، تشبه المقصلة الورقية، ولكنها أكبر حجمًا وأكثر قوة.
بعد ذلك، يُصقل ويُغسل يدويًا. تُزال الشوائب ليبدو الزجاج جميلًا قبل بدء عملية التقوية.
المرحلة التالية هي عملية التقوية نفسها. تُدخل الألواح في فرن وتُبرّد بسرعة إلى درجة حرارة الغرفة. تُحفّز هذه العملية الجزيئات بطريقة تجعل الألواح تتكسر إلى قطع صغيرة بدلًا من شظايا ضخمة.
بعد إخراجها من الفرن، يتم تنظيف ألواح الزجاج مرة أخرى.
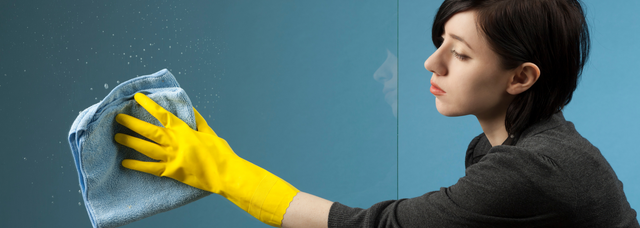
Once the panes are sparkling, the manufacturer moves on to the interlayers. There are three main types of interlayers: PVB, EVA and SGP. We've gone into detail about the differences between laminated glass interlayers before.
الطبقة الداخلية ضرورية للمنتج النهائي، تماماً كأهمية الحشوة لشطيرك المفضل. فبدونها، لن يتمتع الزجاج بخصائصه المميزة.
تُقطع طبقات الصفائح البينية وتُلصق على أول صفيحة من الزجاج المقسّى حديثًا. في البداية، تبدو كغطاء طاولة فضفاض حتى تُقصّ الطبقة البينية لتناسب الزجاج. تُثبّت هذه الطبقة بشريط لاصق قبل عملية التصفيح.
يُغلَق الزجاج بعد ذلك داخل كيس سيليكون ساخن يعمل كطبقة واقية. يُوضَع في الفرن، وتبدأ عملية التصفيح.
تُثبّت دورة التسخين هذه الطبقات معًا بشكل دائم. وهذا الجزء من العملية هو ما يجعل الزجاج الرقائقي الخيار الأمثل للتطبيقات التي تتطلب زجاجًا آمنًا.
تعتمد مدة دورة التسخين على سُمك الزجاج. عادةً، تستغرق حوالي ثلاث أو أربع ساعات.
بعد تصفيح الزجاج، يُترك ليبرد. عندما يصبح ذلك آمنًا، يُزال الشريط اللاصق ويصبح الزجاج جاهزًا للاستخدام.
نبذة تاريخية عن الزجاج الرقائقي
الزجاج الرقائقي هو أحد تلك المنتجات التي ربما لم يتم اختراعها أبدًا لو لم يكن ذلك بسبب حادث سعيد.
كان إدوارد بنديكتوس عالمًا وملحنًا وكاتبًا ورسامًا فرنسيًا. ورغم مواهبه المتعددة، لم يتورع عن ارتكاب الأخطاء.
في أحد أيام عام 1903، كان يصعد سلمًا في مختبر الكيمياء الخاص به، فسقطت قارورة زجاجية عن طريق الخطأ. سقطت على الأرض وتحطمت - على الأقل هذا ما ظنه بنديكتوس.
عند فحصه عن كثب، لاحظ أن القارورة قد تحطمت لكنها حافظت على شكلها. تكسر الزجاج إلى شظايا، لكنها بقيت متماسكة كشبكة عنكبوت شفافة.
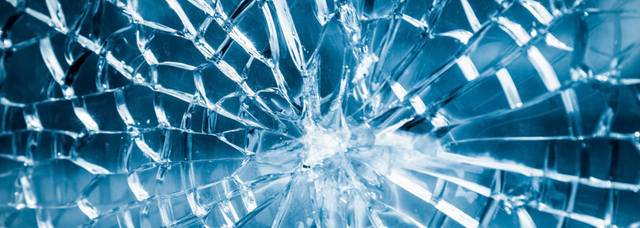
ولأنه عالم، لم يستطع بنديكتوس أن يتجاهل هذا الأمر. أراد أن يعرف سبب انكسار القارورة بهذه الطريقة الغريبة.
أخبره مساعده أن القارورة كانت مليئةً سابقًا بنترات السليلوز. تبخر هذا السائل، لكنه ترك طبقةً رقيقةً شفافة. هذه الطبقة هي التي تماسكت قطع الزجاج.
ربما لم يكن ليفكر في المزيد من هذا الأمر لولا وقوع نوع آخر من الحوادث - وهو ارتفاع عدد حوادث السيارات التي وقعت في باريس في ذلك الوقت.
الزجاج الرقائقي وسلامة السيارة
كان بينيديكتوس يدرك أن الهوس الحالي بالسيارات في شوارع باريس ينطوي على مخاطر. ففي حال وقوع حادث، قد يتحطم الزجاج الأمامي للسيارة إلى شظايا، مما قد يتسبب في إصابات، بل وحتى وفيات.
أدرك أن اكتشافه يمكن استخدامه لجعل السيارات أكثر أمانًا. إذا كانت نترات السليلوز قادرة على صنع قارورة مقاومة للكسر، فلماذا لم يستطع اختراع زجاج أمامي مقاوم للكسر؟
ومن خلال التجربة والخطأ، وجد أن أفضل طريقة للقيام بذلك كانت عن طريق وضع طبقة بلاستيكية بين ورقتين من الزجاج - وهي نفس الصيغة التي نستخدمها اليوم تقريبًا.
ومع ذلك، لم يلق هذا الاختراع رواجًا فوريًا. فمثل العديد من الاختراعات الجديدة، كان إنتاجه بكميات كبيرة مكلفًا للغاية. ومع ذلك، استُخدم زجاج تريبلكس الذي ابتكره في عدسات أقنعة الغاز خلال الحرب العالمية الأولى.
التطورات اللاحقة
في عام 1905، حصل محامٍ إنجليزي يُدعى جون كرو وود على براءة اختراع لنوع من الزجاج الرقائقي لاستخدامه في الزجاج الأمامي للسيارات.
بعد عشرين عامًا، اخترع كيميائيان كنديان مادة PVB، وهي الطبقة البلاستيكية المستخدمة في إنتاج الزجاج الرقائقي حتى يومنا هذا. وسرعان ما تفوق الزجاج الرقائقي المستخدم في هذه الطبقة على الأنواع الأخرى المتوفرة في السوق.
واليوم أصبحت الصيغة هي نفسها إلى حد كبير - ولكنها أصبحت أكثر قوة من أي وقت مضى.
Can you cut laminated glass?
تكمن ميزة الزجاج الرقائقي في أنه شديد الصلابة. تُصعّب الطبقة البلاستيكية البينية قطعه، ولكن يُمكن تحقيق ذلك بشرط عدم استخدام زجاج مُقسّى.
تتضمن الطرق الآمنة طاولات القطع المصممة خصيصًا، ومصابيح النفخ، ونفاثات المياه ذات الضغط العالي، وإطارات المنشار العمودية.
بعد قطع اللوحة، يجب فصل الطبقة الداخلية. غالبًا ما تُصهر بمسدس حراري ثم تُقطع بشفرة.
But remember that toughened glass can
never
be cut. Doing so would cause it to shatter into tiny pieces. That's why laminated glass can only be cut if standard annealed glass interlayers are used.
At ToughGlaze, we provide high-quality,
custom-cut laminated glass to meet your requirements.
Get in touch today for a competitive quote.